Chemical & Process Industry: Technology that will change your business reality (focus on how SAP Business one and ERP will help your business perform better and overcome challenges)
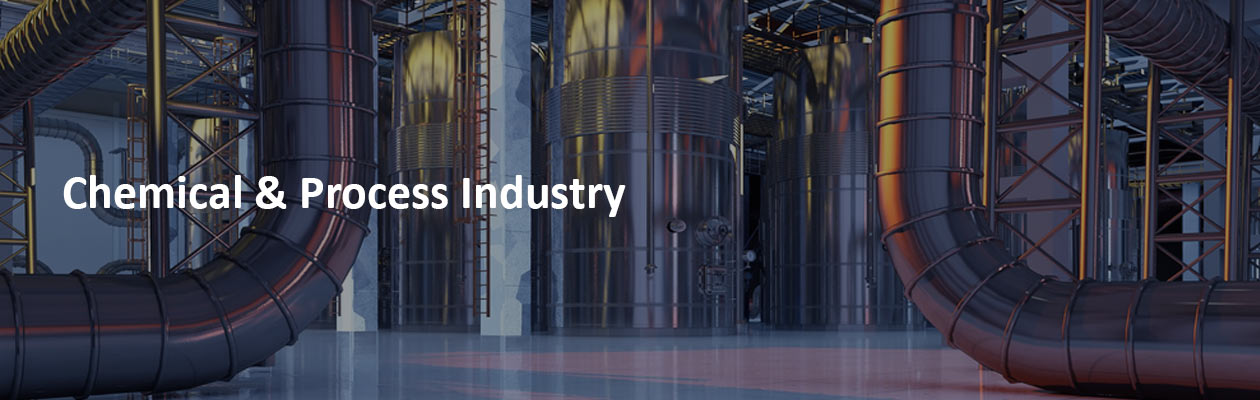
We already know just how quickly the chemicals and process industry is moving. Worldwide sales of chemicals have more than doubled over the last decade, with much of the increase coming from emerging markets.
And at the same time, there’s a fundamental change in approach—with a move from large step-change advances to more specific and personalized innovations.
With a top enterprise resource planning (ERP) software platform like SAP Business One, chemical companies have an opportunity to take great leaps forward. With integrated data, seamless processes, better-informed decision-making, and enhanced collaboration, digital transformation becomes possible.
Gain better outcomes with RPM Infotech’s Process Manufacturing Add-On for SAP Business One:
Our business management software, SAP Business One is a next-generation Intelligent Enterprise Solution designed specifically to meet the needs of chemical manufacturers. It is an end-to-end data driven solution that can help you reimagine your business processes and models by bringing together all your critical data, of supply chain, production planning, manufacturing, and financial systems on one platformwith its mature, affordable and viable Digital Technologies.
Let us have a look at some of the key functionalities of SAP Business One for Chemical Process Industry:
-
Gain visibility: With the help of SAP Business One improve visibility of the production process and order status and make real-time decisions.
-
Better Supply Chain Management: With SAP Business One, a chemical company can work closely with supply-chain members to lower inventory costs, offer more supply chain visibility and efficiency, and reduce cycle time.
-
Batch Production: Create and schedule the optimal number of batch jobs required for a product formula and its multiple packaging configurations, based upon the aggregate demand for the given product.
-
Costing: Roll up existing and theoretical product costs, as well as fixed, tiered and scalable costs to formulas, intermediates and finished goods during product development.
-
Quality: From vendor inspection plans to formula and finished goods QC testing, establish a comprehensive QA program that ensures the delivery of quality products to your customers.
-
Compliance: Keep compliant with industry specific and 21 CFR Part 11 FDA regulations, in terms of labeling, lot traceability reports, transactional audit reports and shipping documentation.
-
Inventory: Manage inventory based upon quality status, units of measure, expiration date, lot number, strength, license, serial number and location to ensure the right inventory is available for manufacturing and distribution activities.
-
Purchasing and Planning: With a granular visibility to available raw material, intermediate and finished goods inventory, as well as current batch production jobs, you can employ economies of scale to purchase raw materials and schedule batch production jobs in order to meet forecasted demand.
With RPM Infotech’s SAP Business One Add-On for Chemical Process Industry, you can:
-
Have complete material traceability
-
Manage production stage wise WIP inventory, its cost and yield management
-
Compliance management with frequent changes in government norms
-
Warehouse management
-
Monitor of BMR / BPR throughout production process
One Master Solution for the Process Industry – SAP Business One:
At RPM Infotech Consulting, we help process industry companies find the right ERP product for their needs. And this can be achieved through the power of SAP Business One ERP solution which gives the process industry complete control over various unit operations, yield calculations and stringent quality norms which is paramount to mitigating the challenges faced by this industry.
SUGGESTED BLOGS
Ten ways to add value to your Discrete Manufacturing Business with SAP Business One
RPM Team2023-05-15T14:29:47+05:30Ten ways to add value to your Discrete Manufacturing Business with SAP Business One Demo [...]
- For Chemical & Process Industry: Technology that will change your business reality (focus on how SAP Business one and ERP will help your business perform better and overcome challenges) Gallery
For Chemical & Process Industry: Technology that will change your business reality (focus on how SAP Business one and ERP will help your business perform better and overcome challenges)
For Chemical & Process Industry: Technology that will change your business reality (focus on how SAP Business one and ERP will help your business perform better and overcome challenges)
RPM Team2023-05-15T14:29:47+05:30Chemical & Process Industry: Technology that will change your business reality (focus on how SAP [...]
Intelligent Enterprise For Next-Gen With SAP Business One
RPM Team2023-05-24T15:01:45+05:30Intelligent Enterprise For Next-Gen With SAP Business One Intelligent Enterprise For Next-Gen With [...]